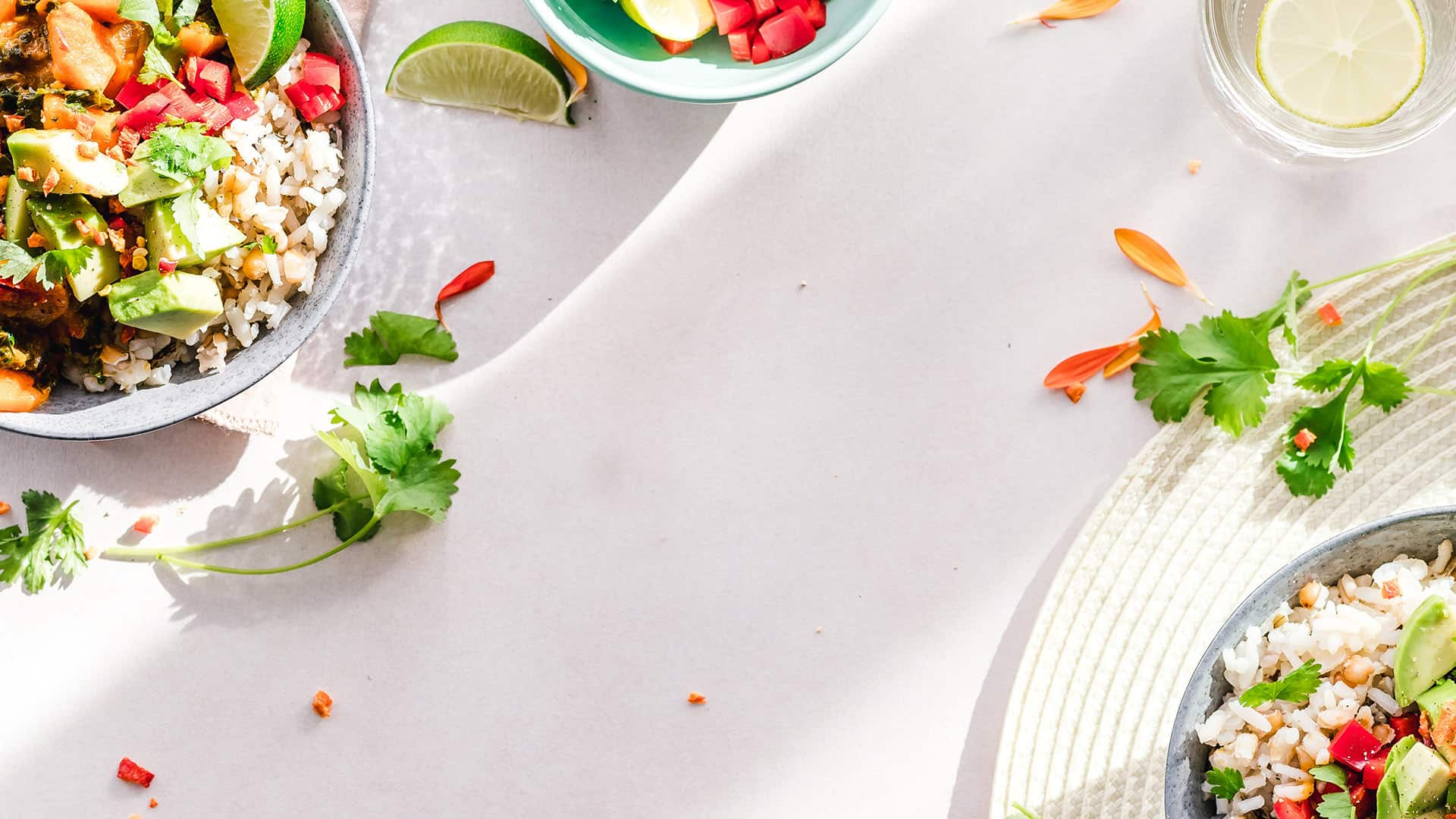
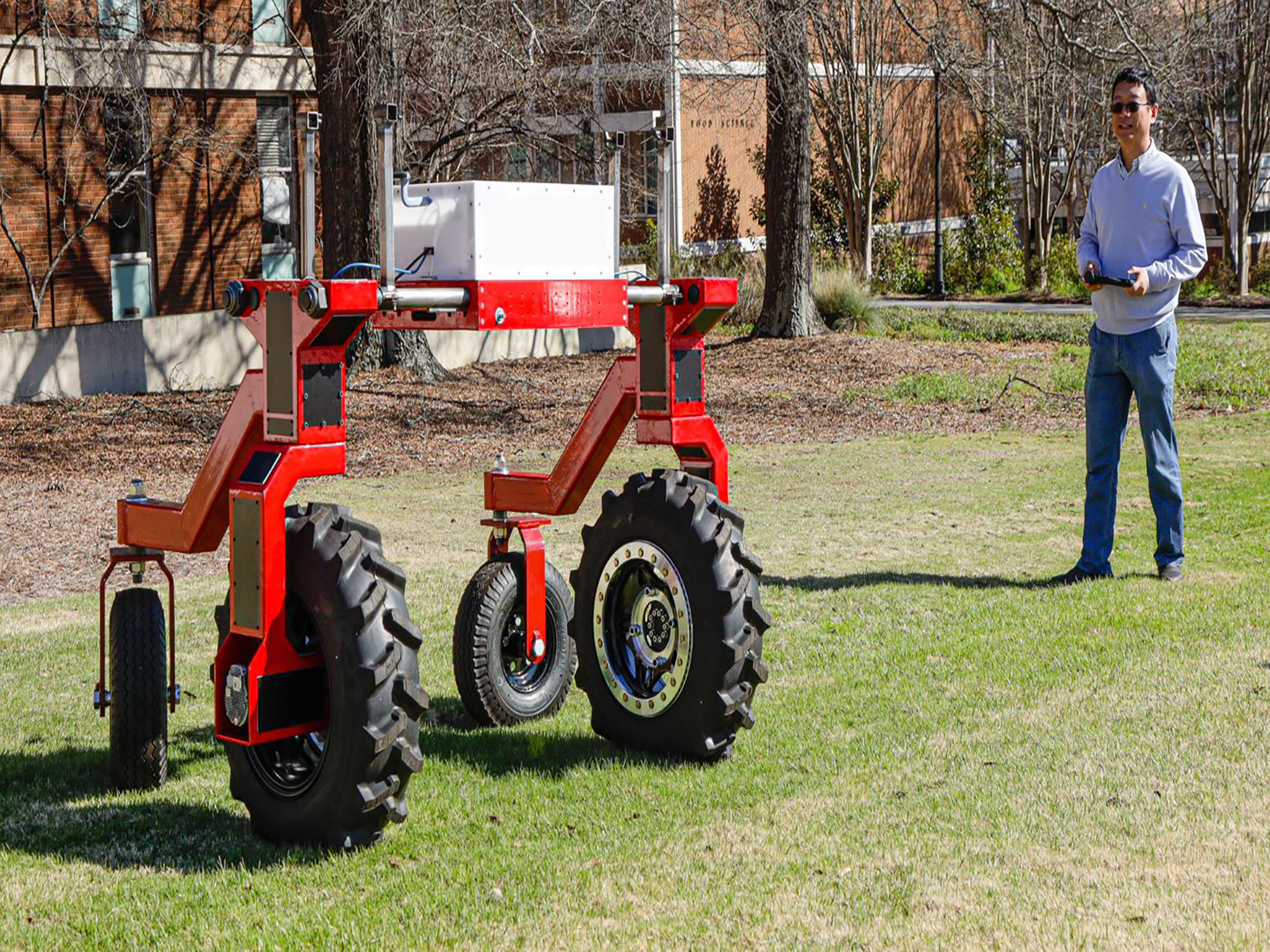
Data science, technology and AI coalesce in the field of plant robotics
A four-wheeled, phenotyping robot that operates autonomously or under human control, Watson is taking shape in Changying 'Charlie' Li’s lab at the Phenomics and Plant Robotics Center (PPRC) on the University of Georgia’s Athens campus in collaboration with researchers in the College of Agricultural and Environmental Sciences (CAES).
Watson’s progress highlights UGA’s pioneering role in integrative precision agriculture, an approach that applies automation technology to farming. The PPRC advances this role by facilitating interdisciplinary, collaborative research at CAES, the College of Engineering and other UGA units.
“Watson can carry sensors and instruments to collect data in the field,” said Li, PPRC Director & Engineering Professor. “We are using three RGB color cameras to collect color images of peanut plants. With those images, we can construct 3D models of the plants and measure morphologic traits such as canopy height, size and volume. The color images can also be used to detect leaf diseases. We plan to add additional sensors, such as a multispectral camera, to measure traits that cannot be measured by color images.”
Photographs snapped by unmanned aerial vehicles (UAVs) help peanut breeders at the UGA Tifton campus measure characteristics of different hybrid peanut genotypes in the field – canopy volume, plant height and plant vigor – that can be seen easier from above than from the ground. But to study smaller details, higher resolution images are necessary, so they are collaborating with Li’s group to incorporate Watson into their phenotyping toolkit.
“We want to develop algorithms and machine-learning techniques to teach robots how to measure disease symptoms to identify susceptibilities as well as hybrids with improved disease resistance,” said Nino Brown, Assistant Research Scientist at CAES.
A key factor for peanut growers is seedling vigor, a genetically influenced function of seedling size after germination that reveals how quickly they develop into larger, more robust and resilient plants.
“If we can accurately measure seedling vigor among plants and hybrid populations, our cultivars or varieties that we release can have some of those high seedling vigor characteristics,” Brown explained.
A human can evaluate a couple hundred plots in a day, but one or two robots or UAVs could evaluate thousands in the same span.
“The more genotypes we can evaluate, the faster and cheaper we’re able to create genetic gain to make significantly improved new peanut varieties,” he added.
In addition, Brown and his colleagues are working out an automated process whereby seeds that will produce peanuts with a high oleic-acid content – which the confection industry prefers for their long shelf life – are identified and separated from those with normal oleic-acid content, used for peanut butter and similar products.
The new process means breeders can have both high-oleic and normal-oleic breeding pipelines, said Brown. “That makes it a lot cheaper for us and provides a high throughput for developing high-oleic varieties.”
CAES agricultural engineer and Professor Glen Rains heads a research group modifying an off-the-shelf soil-sampling robot to perform farm work. The 'Little Red Rover' employs removable attachments for planting seeds, scouting for pests, weed management and harvesting. A multipurpose robotic arm is mounted up front. Sensor data and AI guide the rover’s activities.
Intended for small- and medium-size farms, the rover is designed to be economical, easy-to-use, scalable and rugged. “We’re looking at applications for peanuts and cotton and expect to expand into vegetables as well,” Rains said. “It’s essentially a utility tool like a tractor that could be used year-round, so it wouldn’t have to be sitting in a shed most of the time.”
CAES Assistant Professor and UGA Cooperative Extension Precision Agriculture Specialist, Simer Virk, equips and tests different sensors on standard agricultural machinery that feed performance data to the machine’s in-cab display.
For example, sensors mounted onboard a large planter ensure the desired number of seeds are planted to the prescribed depth and distance apart automatically. Other sensors measure properties such as soil moisture, temperature and organic matter.
If the operator sees that the soil isn’t moist enough for the initial depth setting, “he can act on that information in real time and direct the machine to plant seeds a little deeper", Virk said.
Likewise, when the field’s soil texture changes from clay to sand, the machine operator is notified and can change planting settings while in the field “to maximize the planter performance in each type of soil.”
Automation also enables the precise application of chemicals. Cameras mounted on the sprayer “detect and identify where the weeds are in between the rows, and where the plants are, and turn the nozzles only where they’re supposed to spray,” Virk said.
An innovation originally developed at CAES, variable rate irrigation (VRI) for center-pivot irrigation systems helps producers conserve water and improve efficiency by irrigating crops where and when needed with the exact amount of water required, according to University Professor George Vellidis, Head of the Vellidis Research Group at CAES.
“Sandy soil retains less water than clay, for example, so sandy areas in a field require less water applied more frequently than clay areas do,” he explained. This soil texture information, described by “prescription maps” of the field, is augmented by evapotranspiration data and daily, detailed meteorological forecasts to produce estimates of which specific areas of the field will need water at what intervals and how much to apply. This information is coded into the prescription map.
The estimates are sent to an app on the producer’s smartphone or smart device, which transmits them to the large center-pivot irrigation systems retrofitted with a VRI controller and a GPS receiver. “The GPS tells you where you are in the field so it can translate that position to the map to see how much water should be applied in that location,” Vellidis said.
Agriculture in the future will be smart, precise and more environmentally responsible, Li predicts.
“Being smart means management of the farm and plants will be done autonomously with robots using artificial intelligence, and the process will be self-controlled without human intervention,” he said. “Being precise means that through sensing and automation, crop management can be precisely controlled at the plot or plant level to minimize agricultural input while maintaining maximum output. This can reduce the usage of water, energy, carbon, pesticide and fertilizer to make agriculture more environmentally friendly.”
If you have any questions or would like to get in touch with us, please email
info@futureofproteinproduction.com