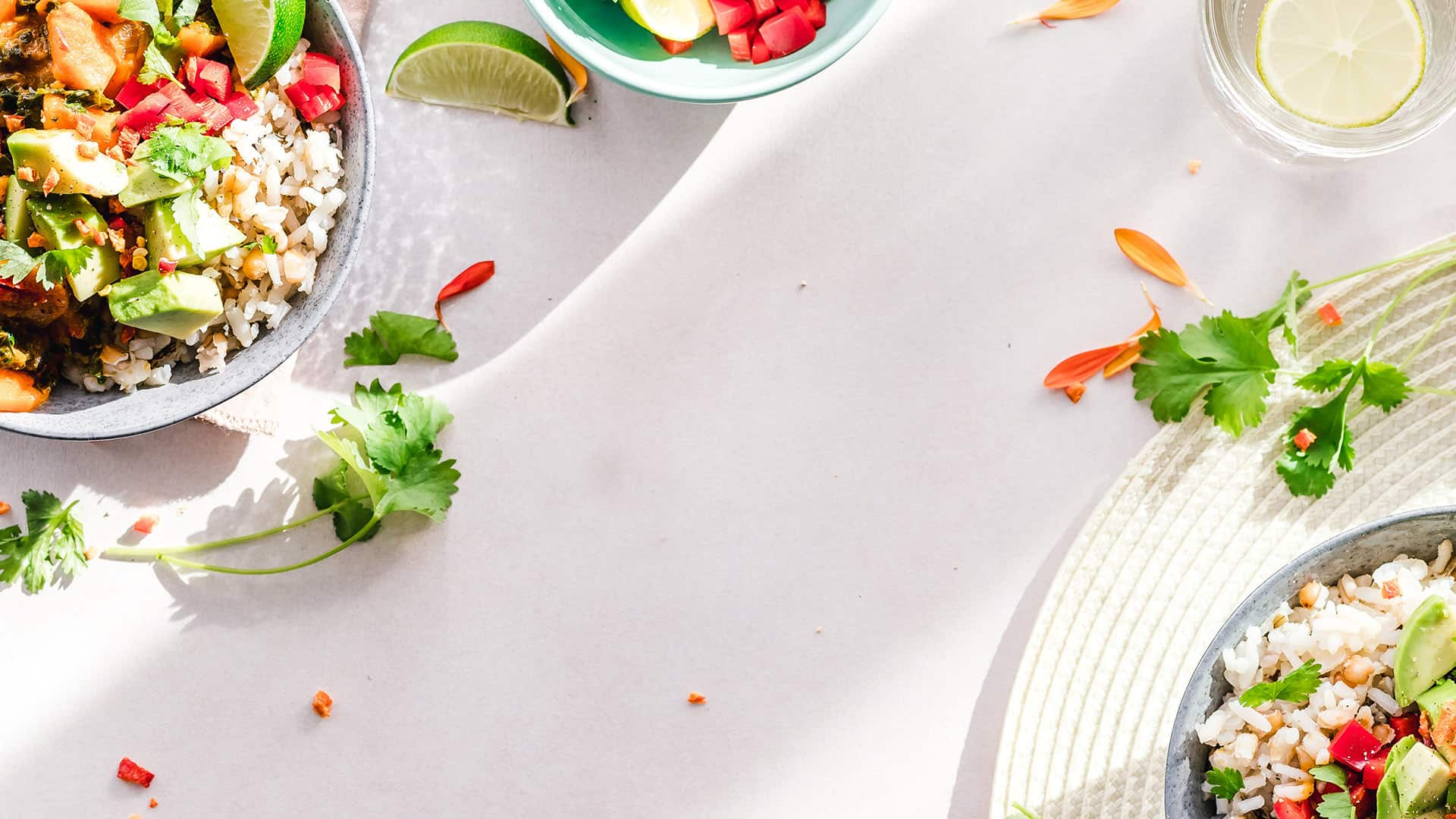
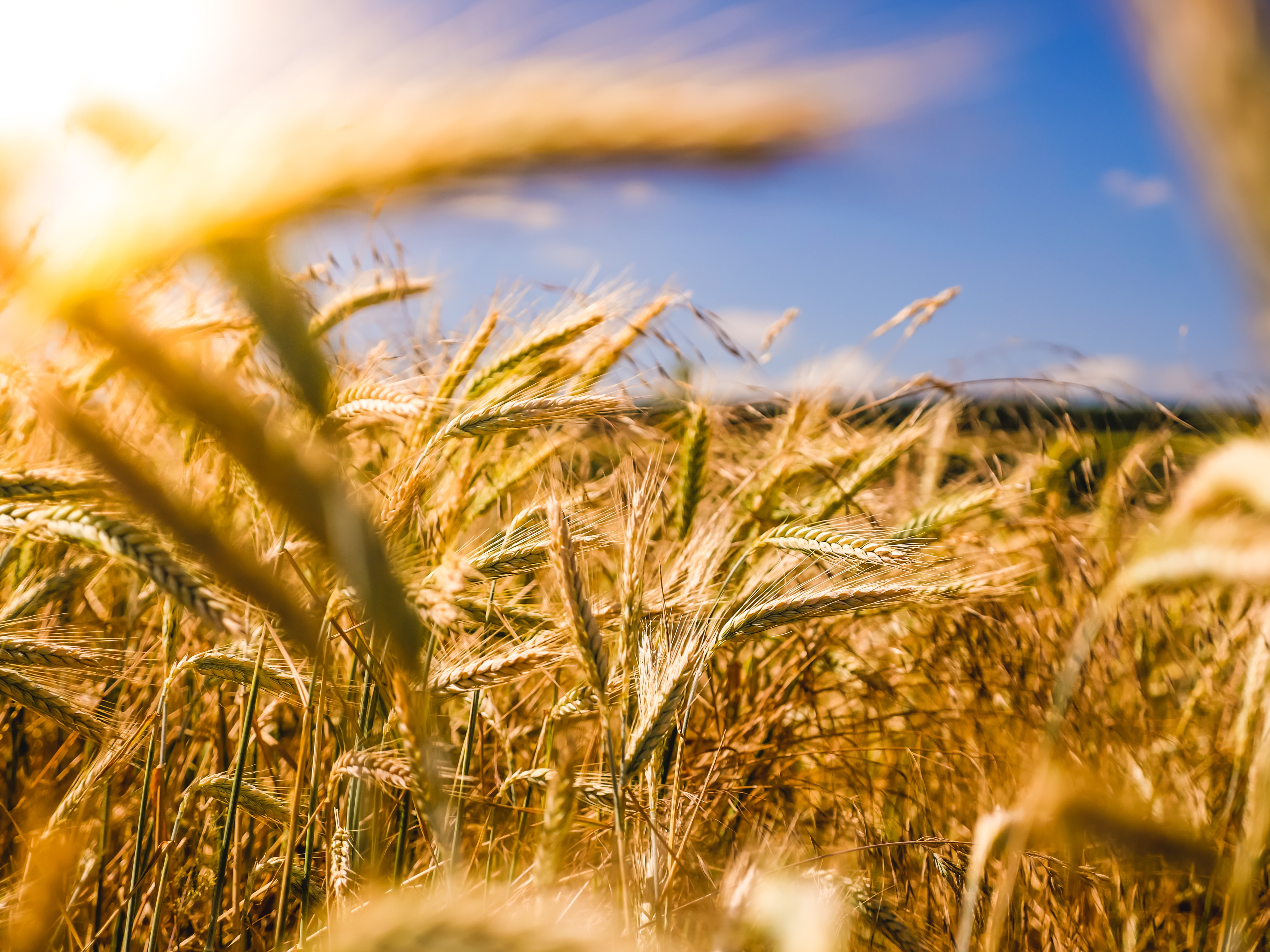
Vertical farming installation for greenhouse growers could help bring the future for Finnish horticulture nearby
It’s a remarkable sight. Trusses of stems hanging sideways over a growing rack, with cucumbers hanging neatly underneath. The goal of this research project is not only to enable growers in Finland to grow cucumbers indoors year-round but also to enable them to minimize the labor on the farms by harvesting automatically with no leaves or stems in the way, simplifying the harvest task for the robot. It is one of the ways the Natural Resources Institute Finland (Luke) helps vegetable growers with the challenges of today and tomorrow. “We need our own strategies to grow.”
Unique circumstances
When it comes to vegetable growing, Finland is a unique country. With its Northern position, providing endless days in summer and endless nights in winter, a length of 1,160 kilometers from north to south, and 5.5 million inhabitants that prefer locally grown food, the circumstances in the fresh produce industry are unlike any other country. “It’s very different from other countries,” Saila Karhu with LUKE institute confirms. Supported by the EU and many Finnish growers, the Research Institute has been helping growers battling these unique challenges for many years. “There will always be some import, but we are helping growers to be as self-sufficient as possible. Finnish consumers want to eat Finnish cucumbers and tomatoes”, she says.
Growing without sunlight became more relevant for indoor growers all over the world but has been something relevant for the Finnish for many years by now. Juha Näkkilä, also a Research Scientist with LUKE Institute, explains how the Finnish have been used to optimize their cultivation with the right lighting recipes for decades due to the lack of natural light in winter times. “Growers always had to calculate how much light they could use and still ventilate the heat away. It’s all about finding the balance between lights, energy costs, and temperature.”
In fact, this research has also been the basis for interlighting, a well-known concept in the industry nowadays. “During our research, we noticed that when we gave light to the whole plant, not just the leaves on top, but also the lower leaves and the stems, production increased, and products were better overall.” The rest is history: interlighting became a common practice in the horticultural industry.
Optimizing lighting strategies and recipes has become increasingly relevant, especially now that electricity prices are rising, comments Pasi Herranen, a researcher of Aalto University cooperating with LUKE. “Growers try their best to minimize the use of their lights. We see how modern techniques can help them. For example, a Finnish research consortium that aims at a system that uses AI to recoup the cultivation costs, only switching the lights on when the electricity price is favorable and turning them off when it is high.” He adds that, in the future, wind power production is expected to grow heavily. “Prices will be more volatile, so with the right techniques, growers can benefit more from this.”
Futureproof
All are examples of how the LUKE institute is developing techniques to futureproof the Finnish greenhouse industry. They have been doing so for many years: for instance, well-known are their research papers calculating the complete CO2 usage of a greenhouse company and even of the entire Finnish industry. It has helped growers lower their emissions, putting the Finnish industry on top of the global list of growers with the lowest CO2 emissions. It’s also a marketing tool for them: packages in supermarkets show how little CO2 the Finnish growers use.
Now Juha and Sailu show the vertical farming installation for greenhouse growers, another investment that might be preliminary currently but could help bring the future for Finnish horticulture nearby.
“Our main goal is not to produce more, although that is very important, but to make working in the industry more comfortable. In the greenhouse, it is very humid and warm, with uncomfortable working conditions. That is why we want to automate as much as possible”, says Saila. “With this solution, we want to further automate growing by removing leaves and doing the harvest at the same time.” The system is patented, and in the future, they will try to grow different crops in the system. “Cucumbers are a pretty easy crop, and the smart hands for packing are already available. It’s much more difficult to harvest strawberries in the field when a robot has to decide which ones to take, with leaves covering the berries.”
“An autonomous greenhouse is what growers want for the future because of the labor shortages,” Juha confirms. “It is also one of our targets: getting that goal within reach by implementing sensors and AI. But it’s not easy. Despite many techniques available, combining them all in the right way will still take many years. People are still very intelligent when you compare them to robots”, she chuckles. “But sensors can also be of great help, supporting the human eye and helping find diseases, for example.”
With the Vertical Farming installation, they expand their knowledge on doing so. Generally speaking, growers in Finland already have quite some experience with Vertical Farming, and the LUKE researchers see opportunities to expand this market further, says Pasi Herranen. “This is because of the climate in Finland. Vertical farms with LEDs provide enough heat to heat the building around them. The excess heat of the farm can be sold to other heating systems, which is not only cutting the cooling costs of the vertical farms but also give growers another tool to make a profit.”
And there are more techniques that could be relevant for other countries as well. Currently, a vertical farm solution developed at Aalto University and made with wood-based elements is being commercialized. “In Finland, there are many wood-based structures and houses. We have successfully used a novel construction techniques called VIS (Vacuum Insulation System) to build a vertical farming pilot, without the need for concrete or plastic.”
The seed funding for commercializing this solution is in full swing. “If it’s this or another solution, we expect in the future that many farms will make use of the options provided by Vertical Farming techniques. Scaling benefits will help bigger farms, whereas smaller companies could supply restaurants or supermarkets.”
Will it also be a solution for the remote living communities in the North of Finland, where currently not many farms are located due to the weather and lack of light? “Cucumbers, for example, are currently more expensive in the north, so that it could be relevant, but you would have to compare the cost to produce there with the cost to drive there. I don’t think that’s calculated yet.”
If you have any questions or would like to get in touch with us, please email
info@futureofproteinproduction.com